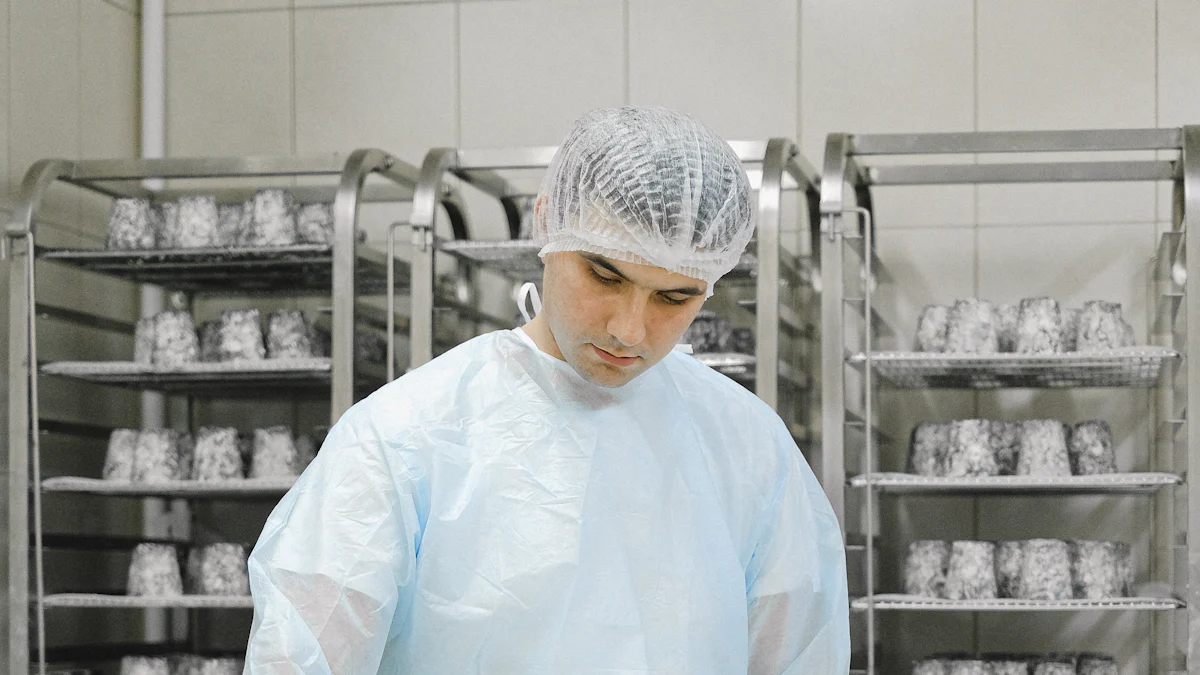
As an animal syringe manufacturer, I understand the critical role quality plays in veterinary care. Every syringe must meet stringent safety and performance standards to ensure the well-being of animals. For instance, thinner needles minimize pain but suit smaller animals, while thicker ones handle larger animals effectively. Ergonomic syringe designs improve handling and reduce discomfort during injections. Innovations like ultra-sharp needles and smart syringes further enhance safety and reliability. By prioritizing these factors, I ensure that each product delivers exceptional performance and meets the diverse needs of veterinarians worldwide.
Key Takeaways
- Quality is paramount in animal syringes; manufacturers must ensure safety and performance to protect animal well-being.
- Selecting high-quality materials like medical-grade plastics and stainless steel is crucial for durability and biocompatibility.
- Rigorous testing, including stress tests and chemical resistance evaluations, guarantees the reliability of syringes before they reach the market.
- Adhering to ISO certifications and veterinary-specific regulations demonstrates a commitment to high manufacturing standards.
- Maintaining sterile environments during production is essential to prevent contamination and ensure the safety of syringes.
- Incorporating ergonomic designs and safety mechanisms enhances usability and reduces the risk of needle-stick injuries for veterinarians.
- Gathering feedback from veterinarians through surveys and direct communication helps manufacturers continuously improve syringe designs.
- Sustainable practices, such as using recyclable materials and reducing waste, reflect a commitment to environmental responsibility in syringe manufacturing.
Material Selection and Testing by Animal Syringe Manufacturers
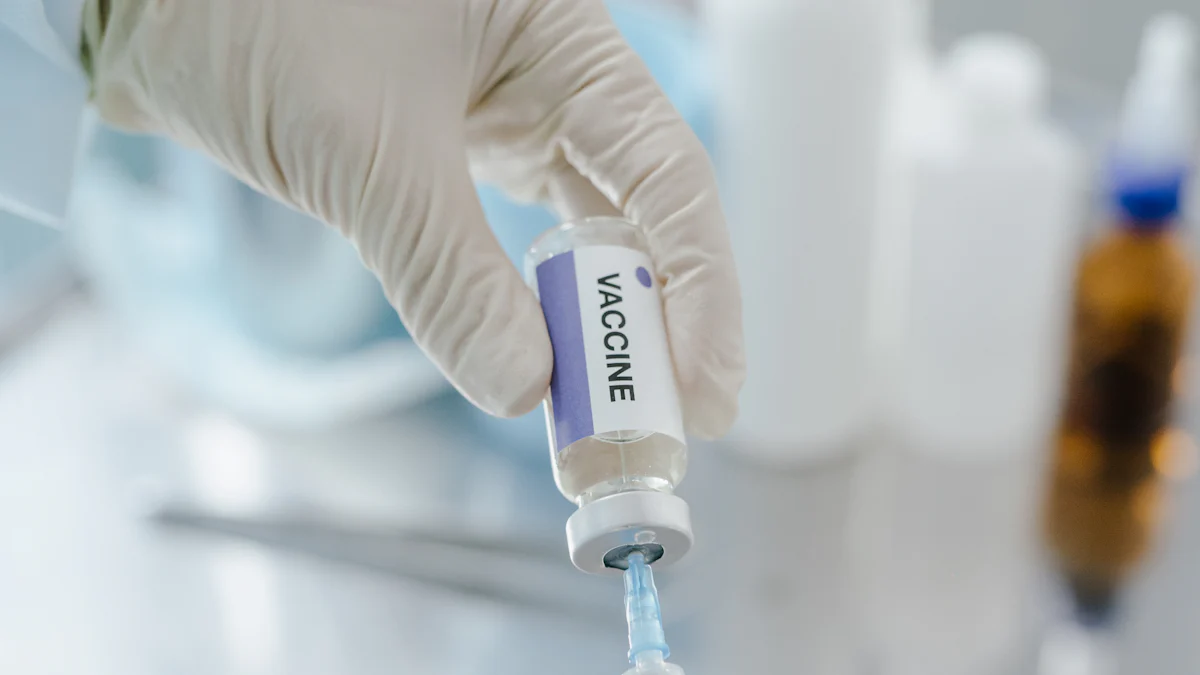
Importance of High-Quality Materials
Types of materials used
As an animal syringe manufacturer, I know that the choice of materials directly impacts the safety and performance of syringes. For this reason, I rely on medical-grade plastics and stainless steel. Medical-grade plastics, such as polypropylene, offer lightweight durability and resistance to chemicals. Stainless steel, on the other hand, provides strength and precision for components like needles. These materials ensure that syringes can withstand repeated use without compromising their integrity.
Ensuring biocompatibility and durability
Biocompatibility is critical in veterinary syringes. I ensure that all materials used are non-toxic and safe for animal tissues. This minimizes the risk of adverse reactions during injections. Durability is equally important. Syringes must endure various conditions, including high-pressure injections and sterilization processes. By selecting robust materials, I guarantee that my products meet the rigorous demands of veterinary care.
Testing Materials for Safety and Performance
Stress testing for durability
To ensure the reliability of syringe materials, I conduct extensive stress tests. These tests evaluate how materials perform under different conditions. Below is an overview of the key tests I use:
Test Type | Description |
---|---|
Elasticity and Recovery | Measures how well the syringe material returns to its original shape after deformation. |
Frictional Resistance | Ensures smooth movement of syringe components to prevent dosing errors. |
Airtightness | Verifies that the syringe seals effectively to maintain sterility. |
Force Distribution | Ensures even application of force across the syringe to prevent localized stress. |
These tests allow me to identify and address potential weaknesses in materials before production begins.
Chemical resistance and sterilization compatibility
Veterinary syringes often come into contact with disinfectants and sterilization agents. I test materials for chemical resistance to ensure they do not degrade or weaken when exposed to these substances. Additionally, I verify that syringes can withstand high-temperature sterilization methods, such as autoclaving. This ensures that the syringes remain safe and effective for repeated use in clinical settings.
By prioritizing material selection and rigorous testing, I uphold the highest standards of quality in every syringe I manufacture.
Manufacturing Standards and Certifications in Animal Syringe Production
Compliance with Industry Standards
ISO certifications for medical devices
As an animal syringe manufacturer, I understand the importance of adhering to internationally recognized standards. ISO certifications, such as ISO 13485, ensure that my manufacturing processes meet stringent quality management requirements for medical devices. These certifications validate that my syringes are safe, reliable, and consistently produced. By following these standards, I demonstrate my commitment to delivering high-quality products that veterinarians can trust.
Veterinary-specific regulations and guidelines
In addition to ISO certifications, I comply with veterinary-specific regulations to meet the unique needs of animal healthcare. These guidelines address factors like syringe size, needle gauge, and material safety for various animal species. I stay updated on these regulations to ensure my products align with the latest industry requirements. This proactive approach allows me to provide syringes that meet the diverse demands of veterinary professionals worldwide.
Importance of Sterile Manufacturing Environments
Cleanroom technology in syringe production
Maintaining sterility during syringe production is critical. I rely on advanced cleanroom technologies to create controlled environments that minimize contamination risks. These technologies include:
- Air filtration systems with HEPA filters to maintain clean air in production areas.
- Structured cleanroom classifications that define cleanliness levels for different production stages.
- Specific gowning requirements to prevent operators from introducing contaminants.
By implementing these measures, I ensure that every syringe meets the highest sterility standards, safeguarding animal health during injections.
Preventing contamination during assembly
Preventing contamination is a top priority during syringe assembly. I use automated systems to handle components with precision, reducing human contact and the risk of contamination. Additionally, I conduct regular inspections to verify that assembly processes remain sterile. These practices ensure that my syringes are safe for use in veterinary settings, where sterility is essential for preventing infections.
By adhering to strict manufacturing standards and maintaining sterile environments, I uphold the quality and safety of my syringes. These efforts reflect my dedication to supporting veterinarians and ensuring the well-being of animals.
Quality Control Processes in Animal Syringe Manufacturing
Inspection and Testing During Production
Automated inspection systems for defects
As an animal syringe manufacturer, I rely on advanced automated inspection systems to detect defects during production. These systems use cutting-edge technologies to ensure precision and reliability. For instance:
- Vision detection systems based on static division identify particles by measuring voltage drops across shadows caused by potential defects.
- High-resolution cameras, combined with image subtraction algorithms, detect cosmetic flaws.
- High Voltage Leak Detection (HVLD) systems identify breaches in sterility by using a high voltage and detection probe.
- Vacuum decay methods test container closure integrity by detecting leaks through pressure changes.
These automated systems also integrate artificial intelligence to enhance accuracy. Platforms like AIM5 combine de-nesting and re-nesting processes with particle and cosmetic defect detection. By employing these technologies, I ensure that every syringe meets stringent quality standards.
Manual quality checks for precision
While automated systems are highly effective, manual quality checks remain indispensable. They complement automated inspections by addressing areas where machines might fall short. For example:
- I conduct manual inspections on syringes rejected by automated systems to determine whether defects are cosmetic or involve foreign materials.
- My team performs these checks immediately after automated inspections to ensure thorough examination.
- Manual inspections are particularly crucial for smaller production batches, where they validate compliance with Good Manufacturing Practices (GMP).
These checks also help verify the performance of automated systems, minimizing false positives and ensuring consistent quality. By combining automation with manual expertise, I maintain a robust quality assurance process.
Post-Production Testing
Leak testing and pressure resistance
Post-production testing is vital for ensuring the integrity and safety of syringes. I employ several methods to test for leaks and pressure resistance:
- Vacuum and pressure decay methods subject syringes to preset conditions to detect leaks.
- High Voltage Leak Detection (HVLD) identifies breaches in sterility with exceptional sensitivity.
- Water leakage testing involves filling syringes with distilled water and applying pressure to check for leaks.
- Air leakage testing uses vacuum conditions to observe pressure changes, ensuring airtight seals.
These tests adhere to ISO standards, guaranteeing reliability and consistency. Deterministic methods like helium leak testing provide non-destructive options for assessing every unit, while probabilistic methods like dye-penetration testing evaluate representative samples.
Packaging integrity and sterility checks
Packaging integrity plays a critical role in maintaining the sterility of syringes during storage and transportation. I use various methods to ensure packaging meets the highest standards:
- Dye penetration and bacterial immersion tests verify the integrity of seals and materials.
- Vacuum decay and high-voltage leak detection assess the packaging’s ability to prevent contamination.
- Distribution and transit testing simulate real-world conditions to evaluate durability during shipping.
- Shelf life and accelerated aging tests confirm that packaging maintains sterility over time.
These rigorous tests ensure that syringes remain safe and effective until they reach veterinarians. By prioritizing quality control at every stage, I uphold my commitment to delivering reliable products for animal healthcare.
Technological Innovations by Animal Syringe Manufacturers
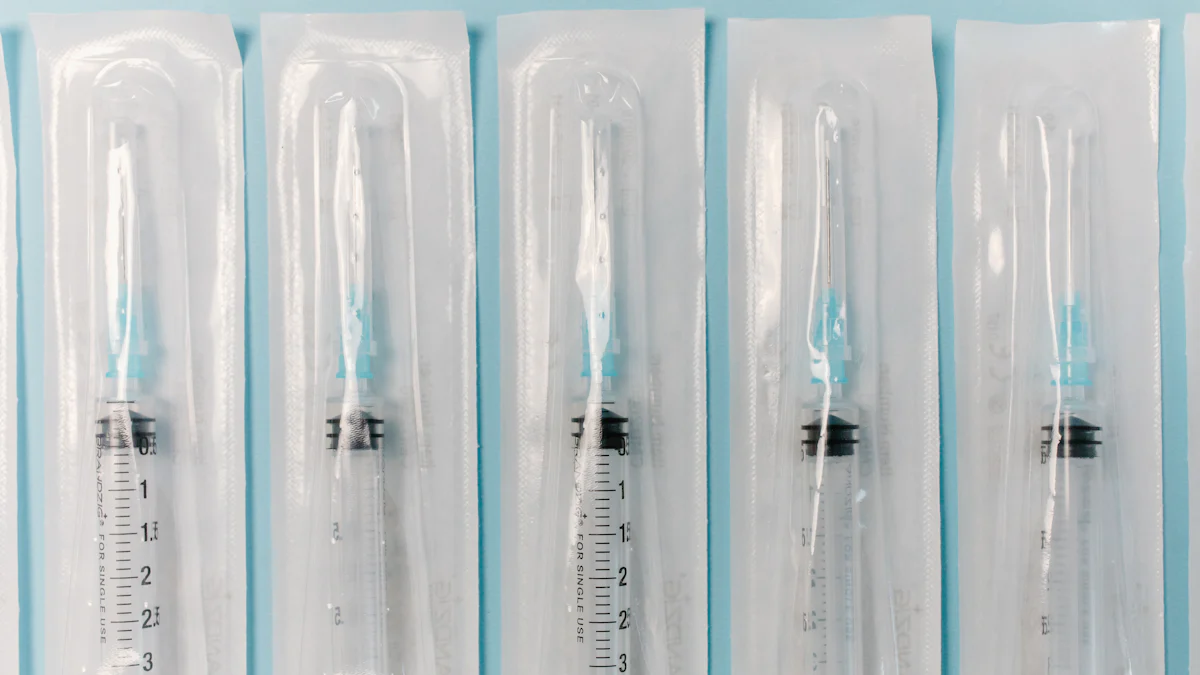
Automation in Syringe Manufacturing
Benefits of robotics in precision and efficiency
As an animal syringe manufacturer, I have embraced robotics to revolutionize production processes. Automation offers several advantages that enhance both precision and efficiency:
- Increased precision ensures consistent and accurate assembly of syringes.
- High-speed automation reduces production time, enabling faster delivery to market.
- Advanced technologies, such as vision validation systems, guarantee that every syringe meets stringent quality standards.
- Cost savings result from reduced labor expenses and minimized material waste.
Robotic systems also streamline workflows, improving defect detection and ensuring compliance with regulatory standards. These innovations allow me to maintain high-quality production while meeting the growing demands of veterinarians worldwide.
Reducing human error in production
Automation plays a crucial role in minimizing human error during syringe manufacturing. By integrating advanced technologies, I ensure consistent assembly and inspection of syringes. Robotic systems reduce operator handling, which lowers the risk of contamination and defects. Enhanced inspection capabilities evaluate visual attributes, weight, and fill volume with unmatched accuracy. This approach not only improves product reliability but also reinforces my commitment to delivering safe and effective syringes for veterinary use.
Advanced Design Features
Ergonomic designs for ease of use
Veterinarians value ergonomic syringe designs that enhance usability and comfort. I prioritize features that improve handling and accuracy during injections. For example:
Ergonomic Feature | Benefit |
---|---|
Ergonomic pencil grip | Enhanced control |
Index finger plunger operation | Precise delivery |
Reduced hand fatigue | Comfort during multiple procedures |
Clear barrel markings | Accurate measurement |
Smooth plunger action | Reduces sudden needle movement, minimizing pain |
These thoughtful designs make syringes easier to handle, reducing hand strain and improving injection accuracy. By focusing on user-friendly features, I ensure that my products meet the practical needs of veterinary professionals.
Safety mechanisms to prevent needle-stick injuries
Preventing needle-stick injuries is a top priority in syringe design. I incorporate safety mechanisms that protect both users and animals. Common features include:
- Retractable needles that automatically retract after use.
- Hinged syringe caps that shield the needle post-injection.
- Safety-engineered blood gas syringes with one-hand activation.
- Re-sheathable winged steel needles for added protection.
- Injection needles with safety features to prevent accidental exposure.
These innovations not only enhance safety but also align with best practices for sharps handling. By integrating these mechanisms, I provide veterinarians with tools that prioritize their well-being and the safety of their patients.
Customer Feedback and Continuous Improvement in Animal Syringe Design
Gathering Feedback from Veterinarians and End-Users
Surveys and direct communication channels
As an animal syringe manufacturer, I prioritize understanding the needs of veterinarians and end-users. To gather valuable insights, I use surveys and direct communication channels. Surveys allow me to collect structured feedback on syringe performance, usability, and design. I design these surveys to be concise and easy to complete, ensuring higher response rates.
Direct communication channels, such as email and phone consultations, provide a more personal approach. These interactions help me understand specific challenges veterinarians face during syringe use. For example, I often receive feedback about the need for smoother plunger action or clearer barrel markings. By maintaining open lines of communication, I ensure that my products address real-world requirements effectively.
Addressing common pain points in syringe use
Feedback often highlights common pain points in syringe use. Veterinarians frequently mention issues like hand fatigue during repetitive injections or difficulty in handling syringes with gloves. I take these concerns seriously and use them as a foundation for improvement. For instance, I have introduced ergonomic designs to reduce hand strain and implemented anti-slip grips for better handling. Addressing these pain points not only enhances user satisfaction but also improves the overall efficiency of veterinary procedures.
Iterative Product Development
Incorporating feedback into new designs
Feedback plays a crucial role in shaping my product development process. I analyze the data collected from surveys and direct interactions to identify trends and areas for improvement. For example, if multiple users request syringes with finer needle gauges for smaller animals, I incorporate this feature into my next design iteration. This approach ensures that my products evolve to meet the changing needs of veterinarians and their patients.
I also collaborate with my design and engineering teams to translate feedback into actionable improvements. Whether it involves refining the syringe’s plunger mechanism or enhancing its durability, I ensure that every modification aligns with user expectations.
Testing prototypes with real-world users
Before launching a new syringe design, I test prototypes with real-world users. I partner with veterinarians to evaluate the prototypes in clinical settings. This testing phase provides invaluable insights into the product’s performance under actual conditions.
Veterinarians assess factors like ease of use, accuracy, and comfort during injections. Their feedback helps me identify any remaining issues and make final adjustments. For instance, if a prototype’s needle retraction mechanism requires additional force, I refine the design to ensure smoother operation. By involving end-users in the testing process, I guarantee that my syringes meet the highest standards of quality and functionality.
Continuous improvement is at the heart of my manufacturing philosophy. By actively seeking feedback and refining my products, I ensure that veterinarians receive tools they can trust for their critical work.
Environmental and Ethical Practices of Animal Syringe Manufacturers
Sustainable Manufacturing Practices
Reducing waste in production
As an animal syringe manufacturer, I recognize the environmental impact of production processes. Reducing waste is a priority in my operations. I have implemented strategies to minimize material waste during manufacturing. For instance, I optimize cutting and molding processes to ensure efficient use of raw materials. Additionally, I recycle production scraps whenever possible, transforming them into reusable resources.
Energy consumption is another area I address. The steel industry, which supplies materials for needle production, is a significant energy consumer. To mitigate this, I adopt energy-efficient technologies in my facilities. These measures not only reduce waste but also lower greenhouse gas emissions, contributing to a more sustainable manufacturing process.
Using recyclable or biodegradable materials
The choice of materials plays a crucial role in sustainability. I prioritize using recyclable and biodegradable materials in syringe production. For example, I incorporate medical-grade plastics that can be recycled after use. This reduces the environmental burden of discarded syringes.
Biodegradable materials are another focus. I explore innovative options that break down naturally without harming the environment. By integrating these materials into my products, I ensure that my syringes align with eco-friendly practices. These efforts reflect my commitment to reducing the environmental footprint of syringe manufacturing.
Post time: Jan-03-2025